Innovations in Conveyor Roller Technology
The evolution of conveyor roller technology has revolutionized material handling in modern industries. From basic designs to advanced innovations, conveyor rollers have become more efficient, durable, and tailored to specific industrial needs. Developments in materials, engineering, and manufacturing processes have led to the creation of specialized rollers that offer enhanced performance and longevity. In today’s competitive market, selecting the right conveyor rollers is crucial for optimizing production efficiency, reducing operational costs, and maintaining a smooth and reliable workflow. Industries such as manufacturing, logistics, mining, and food processing rely heavily on advanced conveyor systems to handle materials effectively. As a result, the importance of investing in high-quality, innovative conveyor rollers cannot be overstated in ensuring operational success and sustainability.
Conveyor Impact Rollers
Innovative Design and Impact Absorption
Conveyor impact rollers, also known as impact idlers, are specifically designed to absorb and mitigate the energy from heavy, abrasive, or sharp materials being loaded onto a conveyor belt. This innovative design typically features a robust central core made from high-strength materials like steel, surrounded by shock-absorbing components such as rubber rings or discs. The outer layer of rubber or similar resilient material effectively cushions the impact of materials, preventing damage to the conveyor belt and reducing wear on the entire system.
Advanced engineering in impact roller design includes features such as:
- Enhanced Rubber Formulations: Utilizing high-performance rubber compounds that offer superior elasticity and durability.
- Sealed Bearings: Ensuring long-lasting performance by protecting the internal components from dust, moisture, and other contaminants.
- Reinforced Cores: Using materials like reinforced steel or composite materials for maximum strength and resilience.
These design innovations ensure that impact rollers can handle the rigorous demands of high-impact loading zones, extending the lifespan of the conveyor system and maintaining operational efficiency.
Key Applications and Benefits
Applications:
1. Mining and Quarrying: Impact rollers are crucial in these industries where heavy rocks and ores are frequently loaded onto conveyors.
- Benefit: They absorb the shock from large, heavy materials, preventing damage to the conveyor belt and reducing maintenance needs.
2. Bulk Material Handling: In industries such as coal, cement, and grain handling, impact rollers manage the heavy impact of bulk materials.
- Benefit: These rollers ensure smooth operation and longevity of conveyor systems, even under heavy load conditions.
3. Construction: Construction sites utilize impact rollers to handle materials like sand, gravel, and rubble.
- Benefit: They protect the conveyor system from the wear and tear associated with moving abrasive and heavy materials.
4. Recycling and Waste Management: Impact rollers are used in recycling facilities where various types of waste materials are loaded onto conveyors.
- Benefit: They cushion the impact of heavy and irregularly shaped waste, preventing damage to the conveyor system and improving operational efficiency.
Benefits:
1. Enhanced Conveyor Belt Protection: Impact rollers prevent costly damage to conveyor belts by absorbing the energy from heavy or abrasive materials, reducing the risk of tears, punctures, and other damage.
2. Reduced Maintenance Costs: By mitigating the impact on the conveyor system, these rollers decrease the frequency and cost of maintenance, leading to lower overall operational expenses.
3. Increased Longevity: The use of impact rollers extends the lifespan of both the conveyor belt and the rollers themselves, ensuring a more durable and reliable material handling system.
4. Improved Efficiency: With reduced downtime and fewer maintenance requirements, impact rollers contribute to a more efficient and uninterrupted workflow, boosting productivity.
5. Versatility: Impact rollers are versatile and can be customized to fit specific conveyor systems and applications, making them suitable for a wide range of industries and material handling needs.
Conveyor impact rollers are essential components that enhance the durability, efficiency, and reliability of conveyor systems. Their innovative design and superior impact absorption capabilities make them indispensable in high-impact environments, such as mining, bulk material handling, construction, and recycling. By investing in high-quality impact rollers, businesses can protect their conveyor systems, reduce maintenance costs, and ensure long-term operational success.
Best Nylon Conveyor Rollers
Innovations and Top Features
1. Advanced Material Composition:
- Feature: The best nylon conveyor rollers are made from high-quality, engineered nylon that offers exceptional strength and durability.
- Innovation: Incorporation of reinforced nylon compounds that enhance load-bearing capacity and resistance to wear and tear.
- Benefit: These advanced materials ensure a longer service life and reliable performance, even in demanding industrial environments.
2. Lightweight and corrosion-resistant:
- Feature: Nylon rollers are significantly lighter than their metal counterparts and highly resistant to corrosion.
- Innovation: Use of lightweight yet strong nylon materials that resist chemicals, moisture, and other corrosive elements.
- Benefit: Reduced overall system weight, lower energy consumption, and suitability for use in humid or chemically aggressive environments.
3. Low-noise operation:
- Feature: Nylon rollers are designed to operate quietly, reducing noise levels in the workplace.
- Innovation: Smooth surface finishes and precision-engineered components that minimize friction and noise generation.
- Benefit: Enhanced working conditions, particularly in noise-sensitive environments such as food processing and packaging plants.
4. High Impact Resistance:
- Feature: Nylon rollers can withstand significant impacts without deforming or breaking.
- Innovation: Reinforcement techniques and the use of impact-modified nylon compounds that absorb shocks effectively.
- Benefit: Improved durability and reduced maintenance needs, making them ideal for heavy-duty applications.
5. Easy Maintenance and Installation:
- Feature: Designed for easy installation and low maintenance requirements.
- Innovation: Modular designs and the use of self-lubricating materials that reduce the need for regular maintenance.
- Benefit: Lower operational costs and minimal downtime, ensuring continuous productivity.
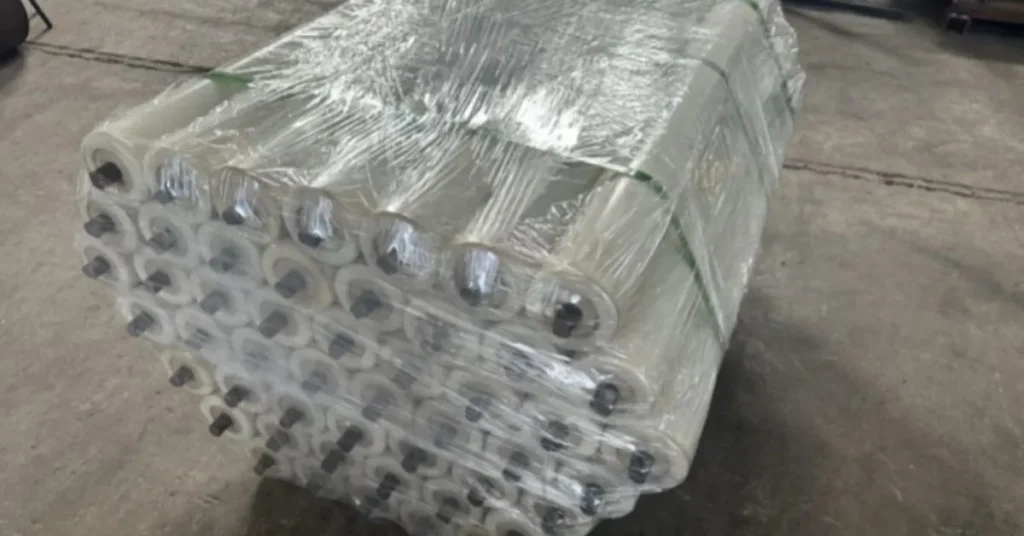
Leading Brands and Models
GRAM Conveyor:
- Model: GRAM Nylon Series
- Features: High-quality nylon material, lightweight, corrosion-resistant, and designed for easy maintenance.
- Benefits: Perfect for industries like chemical manufacturing and cleanrooms, where resistance to corrosive substances is crucial.
Interroll:
- Model: Interroll Polyamide Rollers
- Features: Made from high-strength polyamide, corrosion-resistant, lightweight, and low noise.
- Benefits: Suitable for food processing, pharmaceuticals, and logistics applications due to their hygienic and durable properties.
Rexnord:
- Model: Rexnord 1000 Series Nylon Rollers
- Features: Engineered nylon construction, reinforced core, high impact resistance, and smooth operation.
- Benefits: Ideal for environments requiring quiet operation and high durability, such as packaging and assembly lines.
Flexco:
- Model: Flexco Nylon Rollers HV Series
- Features: High-velocity design, anti-corrosive materials, and precision bearings for smooth and efficient movement.
- Benefits: Designed for high-speed conveyor systems, providing reliable performance and reduced maintenance needs.
Siemens Logistics:
- Model: Siemens Lightweight Nylon Rollers
- Features: High-strength nylon, integrated sensors for real-time monitoring, and energy-efficient design.
- Benefits: Suitable for advanced logistics and automated warehouse systems, offering real-time monitoring and improved efficiency.
Superior Industries:
- Model: Superior Industries Ultra-High Molecular Weight (UHMW) Nylon Rollers
- Features: UHMW nylon construction, excellent abrasion resistance, and low friction.
- Benefits: Ideal for heavy-duty applications such as mining and bulk material handling, providing superior wear resistance and durability.
McMaster-Carr:
- Model: McMaster-Carr Nylon Conveyor Rollers
- Features: A variety of sizes and load capacities; corrosion resistance; lightweight.
- Benefits: Versatile and suitable for a wide range of applications, from light-duty to heavy-duty industrial use.
Hytrol:
- Model: Hytrol Durable Nylon Rollers
- Features: Engineered nylon with reinforced cores, smooth and quiet operation, and high load capacity.
- Benefits: Excellent for use in distribution centers and automated sorting systems, ensuring efficient and reliable material handling.
The best nylon conveyor rollers are characterized by advanced material composition, lightweight and corrosion-resistant properties, low noise operation, high impact resistance, and ease of maintenance and installation. Leading brands like Interroll, Rexnord, GRAM Conveyor, Flexco, Siemens Logistics, Superior Industries, McMaster-Carr, and Hytrol offer top models that cater to various industrial needs. By selecting high-quality nylon rollers from these reputable manufacturers, businesses can enhance the efficiency, durability, and performance of their conveyor systems, ensuring long-term operational success.
Heavy-duty Duty rollers
Innovations in Heavy-Duty Designs
1. Enhanced Material Strength:
- Innovation: Modern heavy-duty conveyor rollers are constructed using high-strength materials such as reinforced steel, hardened alloys, and advanced composites. These materials provide superior load-bearing capabilities and resistance to deformation.
- Benefit: Increased durability and ability to handle extreme weights and harsh conditions without compromising performance.
2. Advanced Sealing Technologies:
- Innovation: The incorporation of advanced sealing technologies, such as triple-lip seals and labyrinth seals, protects the internal bearings from contaminants like dust, water, and chemicals.
- Benefit: Prolonged bearing life and reduced maintenance requirements, ensuring reliable operation in challenging environments.
3. High-Capacity Bearings:
- Innovation: The use of high-capacity, precision-engineered bearings allows heavy-duty rollers to support greater loads and endure continuous operation without overheating or failing.
- Benefit: Enhanced operational efficiency and longevity, reducing the frequency of roller replacements.
4. Impact and Shock Absorption:
- Innovation: Heavy-duty rollers often incorporate shock-absorbing materials and designs, such as rubberized coatings or spring-loaded mechanisms, to mitigate the impact of heavy loads.
- Benefit: Protection of the conveyor belt and roller structure from damage due to heavy or sudden loads, extending the lifespan of the conveyor system.
5. Customizable Designs:
- Innovation: Manufacturers offer customizable heavy-duty rollers tailored to specific industrial applications. This includes varying diameters, lengths, and load capacities to match the exact requirements of different operations.
- Benefit: Optimal performance and efficiency in diverse applications, ensuring that the rollers meet the specific needs of each industry.
6. Corrosion-Resistant Coatings:
- Innovation: Application of corrosion-resistant coatings such as zinc plating, galvanization, or specialized paint formulations to protect the rollers from harsh environmental conditions.
- Benefit: Increased resistance to rust and corrosion, making the rollers suitable for use in outdoor or chemically aggressive environments.
Key Manufacturers and Their Offerings
GRAM Conveyor:
- Model: GRAM Heavy-Duty Series
- Features: High-strength steel construction, impact-resistant design, and advanced sealing for longevity.
- Benefits: Optimal performance in high-impact and heavy-load environments.
- Applications: Mining, quarrying, and large-scale industrial operations.
Interroll:
- Model: Interroll Heavy-Duty Steel Rollers
- Features: Made from reinforced steel, equipped with advanced sealing technology, and capable of handling extreme loads.
- Benefits: Reliable performance in heavy-duty applications such as mining and bulk material handling, with minimal maintenance requirements.
- Applications: Mining, heavy manufacturing, and construction.
Rexnord:
- Model: Rexnord 2000 Series Heavy-Duty Rollers
- Features: Constructed with high-strength alloys, precision bearings, and corrosion-resistant coatings.
- Benefits: Durable and efficient, suitable for continuous operation in harsh environments.
- Applications: Steel mills, heavy-duty manufacturing, and logistics.
Superior Industries:
- Model: Superior Industries Moxie Rollers
- Features: Incorporates shock-absorbing materials, high-capacity bearings, and customizable designs.
- Benefits: Enhanced impact resistance and longevity, tailored to specific industrial needs.
- Applications: Quarrying, mining, and heavy material transportation.
5. Flexco:
- Model: Flexco Heavy-Duty Rollers HV Series
- Features: High-strength construction, advanced sealing technologies, and corrosion-resistant coatings.
- Benefits: Reliable and durable, capable of withstanding extreme loads and environmental conditions.
- Applications: Bulk material handling, recycling, and heavy-duty logistics.
Siemens Logistics:
- Model: Siemens PowerRollers
- Features: Engineered for high load capacities, featuring advanced bearings and robust construction.
- Benefits: Efficient handling of heavy materials with reduced maintenance needs.
- Applications: Automated warehouses, distribution centers, and industrial logistics.
Hytrol:
- Model: Hytrol E24 Heavy-Duty Conveyor Rollers
- Features: Reinforced with high-strength materials, equipped with precision bearings and corrosion-resistant coatings.
- Benefits: Long-lasting performance and reliability in demanding applications.
- Applications: Automotive, heavy manufacturing, and warehousing.
McMaster-Carr:
- Model: McMaster-Carr Heavy-Duty Conveyor Rollers
- Features: Available in various sizes and load capacities, constructed from durable materials.
- Benefits: Versatile and reliable, suitable for a wide range of heavy-duty applications.
- Applications: Heavy equipment manufacturing, bulk material handling, and construction.
Heavy-duty conveyor rollers are essential for applications requiring robust and reliable material handling solutions. Innovations in material strength, sealing technologies, impact absorption, and customizable designs have significantly enhanced the performance and durability of these rollers. Leading manufacturers such as Interroll, Rexnord, Superior Industries, Flexco, Siemens Logistics, Hytrol, McMaster-Carr, and GRAM Conveyor offer a range of high-quality heavy-duty rollers tailored to meet the demands of various industries. By selecting the right heavy-duty rollers, businesses can ensure efficient, reliable, and long-lasting conveyor system performance.
Conveyor Roller with Bracket
New Developments in Bracket Design
1. Adjustable Brackets:
- Innovation: Recent advancements have introduced adjustable brackets that allow for easy modification of the roller height and angle. These brackets are designed with slots and multiple mounting holes, enabling quick adjustments without the need for additional tools.
- Benefit: Flexibility in installation and maintenance, allowing users to fine-tune the conveyor system to accommodate different loads and operational requirements.
2. Modular Bracket Systems:
- Innovation: Modular bracket systems consist of interchangeable components that can be configured in various ways to support different roller types and sizes. These systems often use standardized connectors and mounting points.
- Benefit: Simplified installation and scalability, making it easier to expand or reconfigure conveyor systems as needed without significant downtime or costs.
3. Corrosion-Resistant Materials:
- Innovation: The use of advanced materials such as stainless steel, aluminum, and coated metals in bracket design enhances their resistance to corrosion and wear.
- Benefit: Extended lifespan of the brackets in harsh environments, reducing maintenance costs and ensuring reliable performance in industries like food processing, pharmaceuticals, and chemical manufacturing.
4. Vibration-Dampening Brackets:
- Innovation: Incorporating vibration-dampening materials and design features, such as rubber mounts or shock absorbers, to reduce vibrations transmitted to the rollers and conveyor structure.
- Benefit: Improved roller performance and reduced noise levels, enhancing the overall operational efficiency and creating a more comfortable working environment.
5. Quick-Release Mechanisms:
- Innovation: Brackets with quick-release mechanisms allow for rapid removal and replacement of rollers without the need for complex disassembly.
- Benefit: Minimizes downtime during maintenance and roller replacement, increasing productivity and operational efficiency.
Benefits and Applications
Benefits:
- Enhanced Stability:
Brackets provide a secure and stable mounting point for conveyor rollers, ensuring that they remain firmly in place during operation. This stability is crucial for maintaining smooth and consistent material flow.
- 2. Improved Load Distribution:
Properly designed brackets help distribute the load evenly across the rollers, reducing stress and wear on individual rollers and the conveyor belt. This leads to a longer lifespan for both rollers and the belt.
- 3. Customization and Flexibility:
Adjustable and modular bracket designs offer greater flexibility in configuring conveyor systems to meet specific operational needs. This customization ensures optimal performance and efficiency for various applications.
- 4. Reduced Maintenance Costs:
Innovations such as quick-release mechanisms and corrosion-resistant materials reduce the frequency and complexity of maintenance tasks. This results in lower maintenance costs and less downtime.
- 5. Noise and Vibration Reduction:
Vibration-dampening brackets help to minimize noise and vibrations, creating a quieter and more comfortable working environment. This is particularly beneficial in noise-sensitive industries.
Applications:
1. Manufacturing and Assembly Lines:
- Application: Conveyor rollers with brackets are widely used in manufacturing and assembly lines to transport components and finished products efficiently.
- Benefit: The stability and flexibility of bracket-mounted rollers ensure smooth material flow and accommodate various product sizes and weights.
2. Food Processing:
- Application: In the food processing industry, corrosion-resistant brackets and rollers are essential for maintaining hygiene and preventing contamination.
- Benefit: Stainless steel and other food-grade materials ensure compliance with health and safety standards, while quick-release mechanisms facilitate easy cleaning and maintenance.
3. Pharmaceuticals:
- Application: Conveyor systems in pharmaceutical manufacturing require precise and reliable components to handle delicate and sensitive products.
- Benefit: Vibration-dampening brackets and high-quality rollers ensure smooth and gentle handling of pharmaceutical products, reducing the risk of damage.
4. Logistics and Warehousing:
- Application: Bracket-mounted conveyor rollers are used extensively in logistics and warehousing to move packages and goods efficiently.
- Benefit: Adjustable and modular bracket designs allow for easy reconfiguration of conveyor systems to accommodate changing operational needs and improve workflow efficiency.
5. Chemical and Heavy Industry:
- Application: In industries handling corrosive or heavy materials, robust and corrosion-resistant brackets are essential.
- Benefit: These brackets ensure the longevity and reliability of the conveyor system, even in harsh environments, reducing the risk of equipment failure and operational disruptions.
Conveyor rollers with brackets have seen significant advancements in design, offering new features such as adjustable heights, modular systems, corrosion-resistant materials, vibration dampening, and quick-release mechanisms. These innovations provide numerous benefits, including enhanced stability, improved load distribution, reduced maintenance costs, and noise reduction. The versatility and reliability of bracket-mounted rollers make them ideal for a wide range of applications, from manufacturing and food processing to pharmaceuticals, logistics, and heavy industries. By leveraging these advancements, businesses can optimize their conveyor systems for improved efficiency and longevity.
Impact Roller Compactor
Technological Advancements
1. Enhanced Roller Design:
- Innovation: Modern impact roller compactors feature advanced designs that incorporate heavy-duty steel drums and strategically placed impact zones. These designs maximize ground pressure and compaction efficiency.
- Benefit: Improved soil density and stability with fewer passes, leading to increased productivity and reduced fuel consumption.
2. Variable Impact Energy:
- Innovation: New models are equipped with adjustable impact settings that allow operators to control the force exerted by the compactor. This technology enables precise compaction based on soil type and project requirements.
- Benefit: Enhanced versatility and effectiveness in varying soil conditions, ensuring optimal compaction and reduced risk of over-compaction.
3. Real-Time Monitoring Systems:
- Innovation: Advanced impact roller compactors are fitted with GPS and real-time monitoring systems that provide data on compaction progress, ground conditions, and machine performance.
- Benefit: Increased operational efficiency through real-time feedback, allowing for immediate adjustments and ensuring consistent compaction quality.
4. Hydraulic Systems:
- Innovation: The integration of sophisticated hydraulic systems allows for smoother and more efficient operation, with precise control over the roller’s movements and impact energy.
- Benefit: Improved fuel efficiency, reduced wear and tear on the machinery, and enhanced operator comfort.
5. Eco-Friendly Technologies:
- Innovation: Manufacturers are incorporating eco-friendly technologies such as low-emission engines and biodegradable hydraulic fluids to reduce the environmental impact.
- Benefit: Lower carbon footprint and compliance with stringent environmental regulations, making the equipment suitable for eco-sensitive projects.
Uses and Benefits in Various Industries
Construction:
- Uses: Impact roller compactors are widely used in the construction industry for compacting soil, gravel, and asphalt in road construction, foundations, and other infrastructure projects.
- Benefits: Efficient Compaction: Achieves high levels of compaction quickly, reducing the number of passes needed and speeding up project timelines.
- Improved Load-Bearing Capacity: Enhances the stability and load-bearing capacity of construction sites, ensuring long-lasting and durable structures.
Mining:
- Uses: In mining operations, impact roller compactors are utilized for compacting haul roads, reducing the risk of ground failure and improving the efficiency of heavy machinery.
- Benefits: Enhanced Safety: Creates stable and even surfaces for mining equipment, reducing the risk of accidents and improving operational safety.
- Reduced Maintenance: Well-compacted roads reduce wear and tear on mining trucks and machinery, leading to lower maintenance costs and extended equipment life.
Landfill and Waste Management:
- Uses: These compactors are employed in landfill sites to compact waste materials, maximizing space utilization and enhancing site stability.
- Benefits: Increased Site Capacity: Maximizes the use of available space by compacting waste efficiently, extending the lifespan of landfill sites.
- Environmental Compliance: Helps meet regulatory requirements by ensuring proper waste compaction and reducing the risk of environmental contamination.
Agriculture:
- Uses: Impact roller compactors are used in agricultural settings for soil preparation, improving soil structure, and enhancing irrigation efficiency.
Benefits:
- Soil Health: Promotes better soil aeration and water infiltration, leading to healthier crops and improved agricultural yields.
- Erosion Control: Stabilizes soil and reduces erosion, protecting valuable topsoil and maintaining land productivity.
Energy Sector:
- Uses: In the energy sector, particularly for wind farms and solar installations, compactors are used to prepare the ground for infrastructure development.
Benefits:
- Foundation Stability: Ensures a stable foundation for energy installations, reducing the risk of ground shifting and structural damage.
- Efficient Installation: Speeds up site preparation, allowing for quicker deployment of energy infrastructure.
Urban Development:
- Uses: Impact roller compactors play a crucial role in urban development projects, including the construction of parks, recreational areas, and commercial developments.
Benefits:
- Enhanced Site Preparation: Provides a stable base for various urban infrastructure projects, ensuring longevity and durability.
- Noise Reduction: Modern compactors are designed to operate quietly, minimizing noise pollution in urban areas and contributing to better community relations.
Impact roller compactors have seen significant technological advancements, including enhanced roller designs, variable impact energy, real-time monitoring, sophisticated hydraulic systems, and eco-friendly technologies. These advancements have expanded their uses and benefits across various industries, including construction, mining, landfill and waste management, agriculture, the energy sector, and urban development. By leveraging these innovations, industries can achieve more efficient, effective, and environmentally friendly compaction, leading to improved project outcomes and operational efficiencies.
Innovations in conveyor roller technology, such as advanced materials, precision engineering, and smart monitoring systems, have significantly enhanced the efficiency, durability, and performance of conveyor systems. Developments in nylon and impact rollers, heavy-duty designs, and the integration of adjustable and modular brackets have revolutionized material handling across various industries. Looking ahead, the future of conveyor rollers will likely see further advancements in eco-friendly materials, real-time data analytics, and automation integration, driving greater operational efficiency and sustainability. Emerging trends include the adoption of smart sensors for predictive maintenance and the use of advanced composites for lightweight yet robust rollers. These innovations will continue to optimize conveyor systems, ensuring they meet the evolving demands of modern industry.